
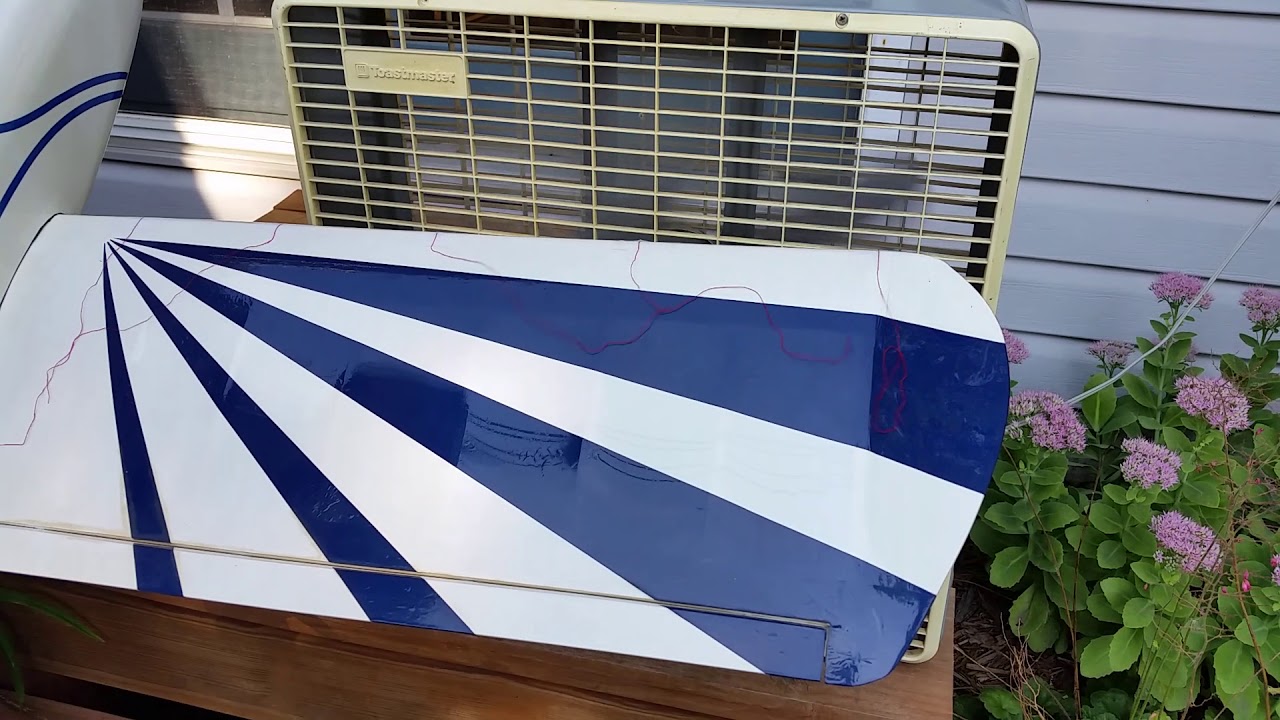
There are many sources for unsteady fluid forces in a turbo-machine, as reviewed by Srinivasan (1997).
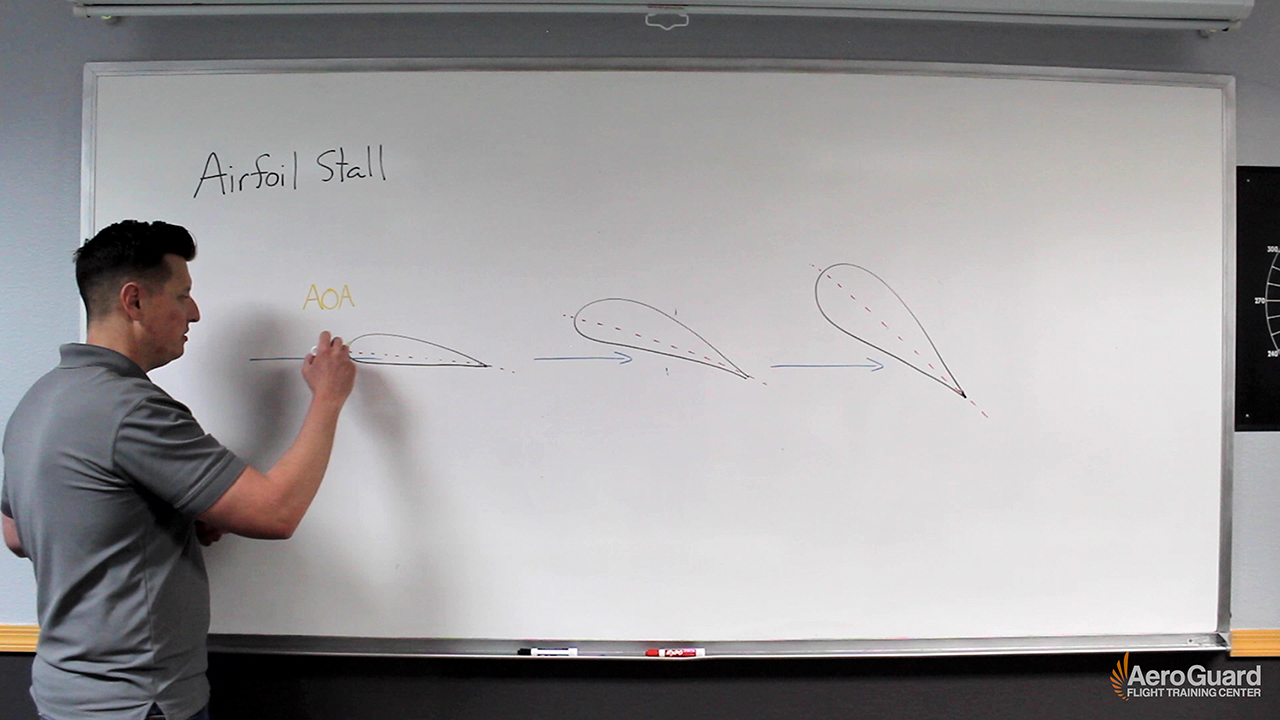
These vibrations are detrimental both for the structural integrity of the blade and the overall machine performance. Turbomachinery blades are subjected to unsteady fluid-mechanical forces and these can lead to blade vibrations. The phase of the shear layer motion with respect to the airfoil motions shows a clear difference between the exciting and the damping case. On the other hand, the shear layer formed after separation is found to clearly move periodically away from the airfoil suction surface and towards it with a phase lag to the airfoil oscillations. Particle Image Velocimetry (PIV) measurements of the flow around the oscillating airfoil show that the shear layer separates from the leading edge and forms a leading edge vortex, although it is not very clear and distinct due to the low oscillation amplitudes. Outside this range of reduced frequencies, the energy transfer is negative and under these conditions the oscillations would be damped. These measurements indicate that for large mean angles of attack of the airfoil ( α m), there is positive energy transfer to the airfoil over a range of reduced frequencies ( k=πfc/U), indicating that there is a possibility of airfoil excitation or stall flutter even at these low Re ( c =chord length). The unsteady loads on the oscillating airfoil are directly measured, and are used to calculate the energy transfer to the airfoil from the flow. The airfoil is placed at large mean angle of attack ( α m), and is forced to undergo small amplitude pitch oscillations, the amplitude (Δ α) and frequency ( f) of which are systematically varied. There is virtually no effect of the compliant flag on the mean lift at small angles of attack.In the present work, we experimentally study and demarcate the stall flutter boundaries of a NACA 0012 airfoil at low Reynolds numbers (Re∼10 4 ) by measuring the forces and flow fields around the airfoil when it is forced to oscillate. The oscillation frequencies of the flag are in the same range of vortex shedding frequency of the baseline airfoil, suggesting that the wake resonance mechanism may be behind the observations of the enhanced lift at the post-stall angles of attack. The flag oscillations occur mostly in the first structural mode, while the higher modes reveal the three-dimensionality of the flag displacement field. The instantaneous flow and the range of oscillation frequency have strong similarities to those of the active flow control methods for separation, yet this is a passive flow control method that relies on unsteady effects. Leading-edge vortex shedding and formation of a separation bubble are observed when the flag tip reaches around the maximum displacement. The limit cycle oscillations of the flag between the airfoil surface and the freestream have a dominant frequency and promote reattachment of the flow, producing a remarkable increase in the maximum lift coefficient and stall angle.
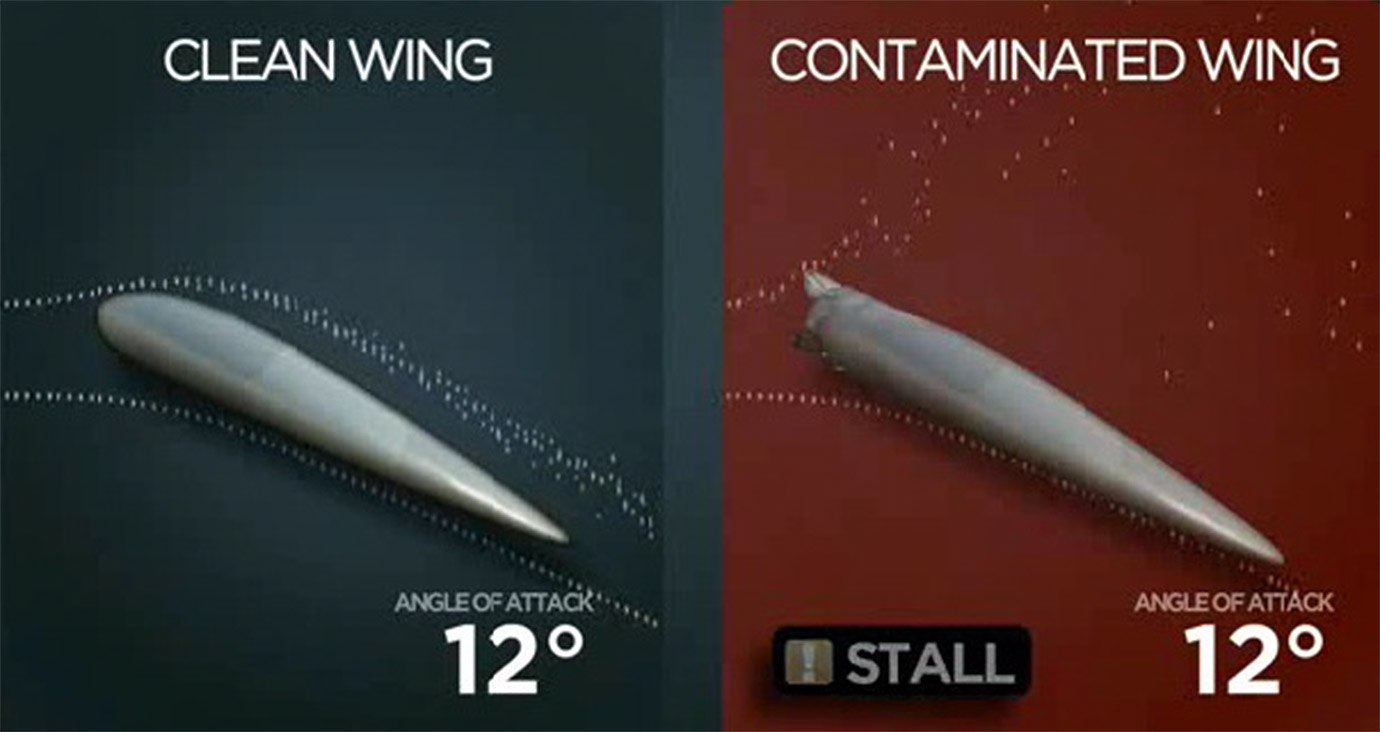
We present experiments demonstrating that a small flag attached to the surface of an airfoil near the leading edge exhibits self-excited oscillations when the airfoil is set at a post-stall angle of attack.
